About 50 years ago, the application principle of a 5-roll coating station for the coating of solventless, thermal-curing silicones was launched onto the marketplace and replaced, to a vast extent, the offset gravure system, which often still is operated with solvent-based silicones.
Since then, the 5-roll coating principle became the standard coating method for siliconized substrates; i.e., for either paper or polymer films processed at speeds exceeding 200 mpm and in working widths ranging mainly from 1,300 to 2,100 mm. Nowadays, coating stations with even six smooth rolls for highspeed applications exceeding operational speeds of 800 mpm are quite common, but the difference in the setup and arrangement of the rolls is not limited to just one more roll. The features of the 5- and 6-roll process are discussed in this article.
For the application of water-based, pressure-sensitive adhesives (PSAs), a pressurized, chamber doctor-blade system or a curtaincoating process usually is used. These two methods differ in their basic working and application principle – and so does the day-to-day operation.
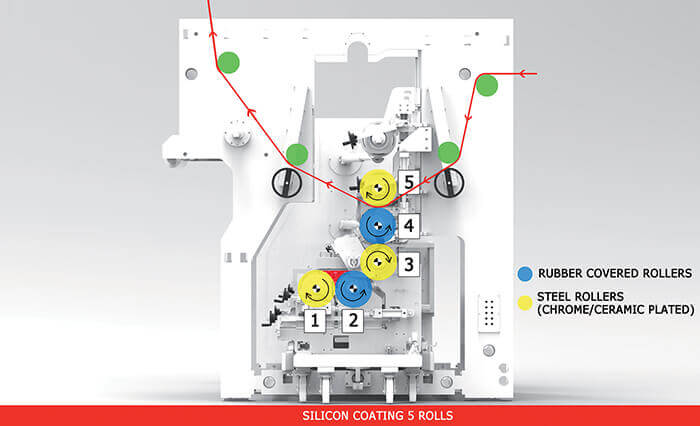
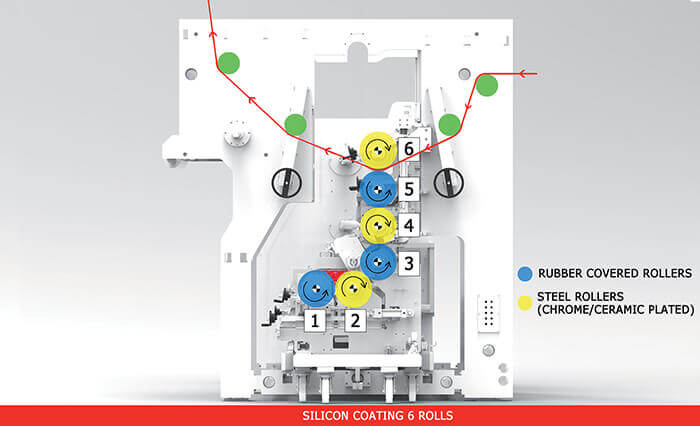
1. Application of solventless silicones by multi-roll technology
Considerations in regard to the metering roll No. 2: In reviewing Figures 1 and 2, a major difference concerning the metering roll No. 2 is obvious. In the 6-roll station, the roll No. 2 is a high-precision, chrome or ceramic, plated-steel roll with accuracies of approx. 2-μm T.I.R., whereas the corresponding roll in the 5-roll station is a rubber-covered roll with about 18-μm T.I.R. Hence, the achieved coatweight accuracies in CD and MD with a 6-roll station are higher; also, there is significantly less wear compared to the rubber-covered roll in the 5-roll station.
Aspects of coating-width change
In principle, there are several ways to change the coating width:
1. Adjustable side dams placed between rolls No. 1 and 2 allow a quick changeover from wide to narrow. The areas where the side dams are set to the rolls need to be well lubricated. The main disadvantage, however, are the dry roll areas or edges caused by a narrow coating width, which will wear the roll surface and lead to needing to change the rubber-covered roll when going from narrower to wider widths.
2. Front side dams placed at the front side of rolls No. 1 and 2 are used to seal the nip. In this case, sufficient lubrication is needed. However, both rolls are moistened constantly as the edge scrapers on roll No. 3 adjust the coating width (5-roll station). The scraped-off and filtered silicone is fed back to the reservoir or to the nip.
3. As a standard of the 6-roll station, besides roll No. 5, roll No. 3 can be executed as a sleeve system. This enables the operator to quickly change the working/coating width and scraper settings or a feedback circuit of the silicone is not needed. Contamination of the silicone and time-consuming scraper adjustments, which also may lead to coating defects, are eliminated. The sleeves of rolls No. 3 and 5 can be accommodated easily by one operator in less than three mins without cutting the web. Contact time and efficiency of the machine are increased.
Comparison of circumferential speeds
With the use of solventless silicones and with an increase of the operational speed of the line, a higher tendency of misting occurs. The working principle of the multi-roll coating technology is based on forward-turning rolls, which spread the silicone media by differential rolls’ speeds, from the metering gap between rolls No. 1 and 2 up to the coating roll – either roll No. 4 or 5 (see Figures 1 and 2). Silicone suppliers already have done extensive work to limit the appearance of misting. But, by adding one more roll, the circumferential speeds of rolls No. 2, 3 and 4 are reduced in the 6-roll station, which further limit the appearance of misting on the one hand but also facilitate the daily operation of the line on the other.
Caused by a slower speed of the roll No. 2, the turbulences occurring in the metering gap between rolls No. 1 and 2 are reduced, limiting risk of air entrapment. In addition, higher coatweight accuracies of approx. +/-0.04 gsm or even better in CD and MD are achieved, along with the possibility to exceed coating speeds of 800 mpm.
As an example, Tables 1 and 2 show the approximate roll speeds related to the operational speed (100%). Reference is made to 800- mpm coating speed with 1-gsm application of solventless silicone.
Of course, the diameter of the coating rolls also influences the misting effect. Machinery suppliers chose the diameter of the rolls dependent from the working width and the targeted operational speed of the line; for instance, up to 1,650 mm wide, a diameter of 250 mm is chosen. For lines exceeding this width, roll diameters of 300 mm are implemented.
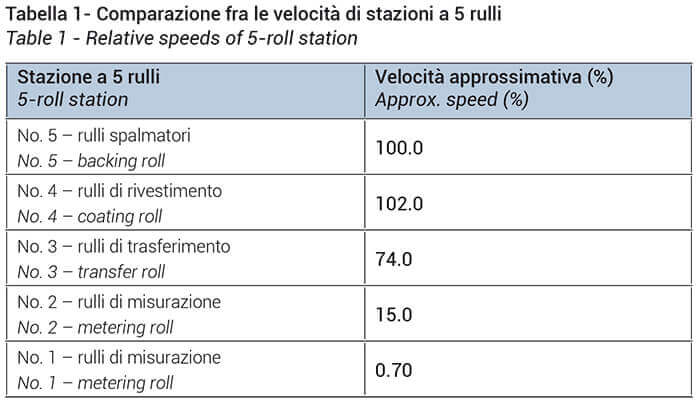
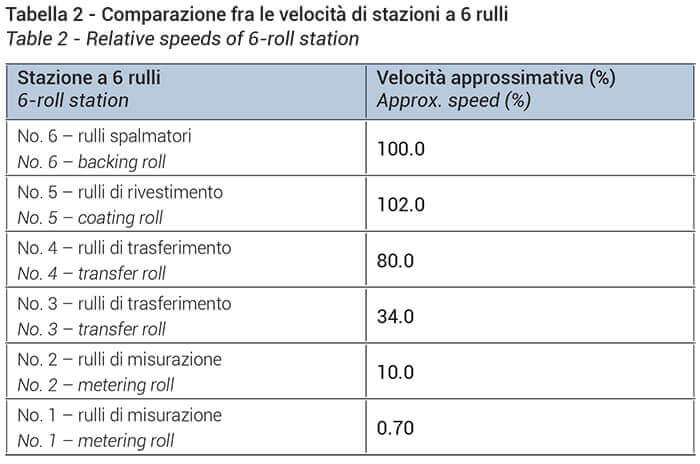
Roll adjustment
Depending on the speed of the line, the working width and the coating accuracy required, a 5-roll station can be equipped either with pneumatically or hydraulically adjusted rolls, whereas a 6-roll station is designed solely with hydraulic adjustment due to the higher dynamic forces.
Roll tempering (heating/cooling)
The operating speed of a 5-roll station is lower compared to the 6-roll station. Less heat, generated by friction, is occurring, and a more simple cooling of the rolls is required; i.e., the tempering is limited to three rolls. Common for the 6-roll station is the use of three independent water-tempering circuits connecting – for instance – rolls No. 1 + 2; 4; as well as No. 3 + 5 + 6. One additional tempering circuit might be used for the silicone-mixing units and holding tank. Heating of the silicone might be needed when production with a fresh silicone is started to ensure constant coating environments, but cooling is mandatory.
Investment costs
The additional costs arising from a 6-roll station are comparatively low, relative to the total investment costs of a complete line and compared to the station’s benefits. The ROI is reached quickly, especially due to the higher coating accuracy, the quick changeover from paper to film or vice versa, and the faster change in working width.
Similarities
Of course, all rolls are individually driven, adjustable – either manually or motorized – and usually guided in linear bearings. A quality criteria of the coated product is the bending compensation of roll No. 1 in traverse direction (skewing), which is conducted by means of a variable adjustment to ensure an accurate pressure line in the metering gap between rolls No. 1 and 2.
Extensions
The multi-roll station can be executed as a simultaneous coating station by applying silicones (also with different properties) to the front and backside of the substrate. After the coating process, the substrate is guided to an approximately 90°-angled air cushion, feeding the substrate in the horizontally arranged airfloatation dryer.The previous discussion is summarized by Table 3, which compares various specifications for 5- and 6-roll coating stations.
2. Application of water-based PSA with pressurized chamber doctor system and curtain-coating method
Generally, there are various methods to apply water-based PSA to the siliconized substrate. In this article, we are focusing on two processes: Pressurized- Chamber Doctor (PCD) with gravure roll and Curtain Coating. The latter is a pre-dosed system; i.e., quantity applied to the substrate is defined and controlled by the media supply system and for 100% application (no return flow). In opposition, PCD is a so-called self-dosing system; i.e., the quantity of media applied is defined and can be controlled by the coating system itself.
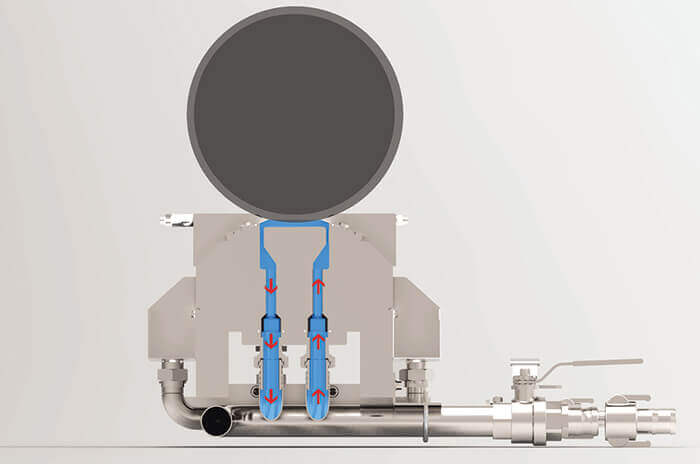
Pressurized-chamber doctor system
The main features of the PCD are as follows:
- Various coatweights with one gravure roll are possible (approximately ≤40%) due to change in revolutions of pump for media supply, resulting in a controlled overfilling of the engraving;
- High coating speeds are possible, also exceeding 800 mpm;
- No air entrapment; i.e., no bubbles, foam or micro-foam (especially important for transparent and optical facestock materials);
- Minimal media content in the chamber;
- Two pressure sensors;
- Constant coatweights during acceleration and decrease of operational speed;
- High coatweight accuracy (≤3% dry);
- Change of blades without tools;
- Chamber doctor in stainless steel or anodized aluminum;
- Use of chrome- or ceramic-plated gravure rolls with various diameters. The blades are of corresponding material (steel or ceramic);
- Tempering (i.e., cooling or heating) of the gravure roll and chamber;
- Quick changeover of media;
- Simultaneous, double-sided coatings are possible.
Besides a high media throughput, the use of a tri-helically engraved roll in reverse operation – as well as an applied pump pressure between 50 and 600 mbar within the chamber doctor – are preconditions in the design of the PCD (see Figure 4). The chamber can be arranged in the 3, 6 or 9 o’clock position to the gravure roll. Also important is the definition of the design of the tri-helically engraved roll in regard to the angle (usually 30- 80%), as well as the ratio of engraved and non-engraved areas, which determines the standard coatweight of the system. Media ≤1,500 mPas (including tackifiers) and high solids ≤65% can be applied.
Curtain coating (Contour coating)
With this pre-metered system, a highprecision slot die is mounted at a distance of typically approximately 10-20 cm above a horizontally guided substrate (see Figure 5). The web is guided around a chrome-plated steel counter roll. A pulsation-free pump feeds the media to the slot die, where it is distributed equally across the width. The coating media leaves the die, freely falls across the web width and forms a curtain. The coating point is adjustable and ranges between the 11 and 1 o’clock position.
Preconditions for the curtain-coating method are as follows:
- Minimum flow rate is approximately 6 liters/min, related to a 1-meter die width (minimum needed to build up a stable curtain);
- Caused by the surface tension of the media, its contracting is observed as it leaves the die. The edges of the curtain must be guided vertically, also for avoiding an edge buildup on the substrate;
- Caused by a too-low viscosity, the so-called heel formation (i.e., backflow of the media) can occur. Viscosities at high shear rates between 50-400 mPas are recommended;
- The dynamic surface tension of the media should be as low as possible (about 30 mN/m). With a too-high surface tension, the curtain might be unstable at the given flow rate, potentially contract too much or not form at all. Also, the wetting process at the coating point might be disturbed;
- The coating media typically needs to be degassed as larger air bubbles may rupture the curtain. Smaller bubbles might interfere with a smooth coating surface, as well as during the drying process;
- The boundary air layer on the substrate especially at higher speeds has to be removed by a vacuum suction device right before the coating point to avoid distortions and to stabilize the heel;
- Substrate properties (hydrophilic/hydrophobic/wetting/ topography, etc.) and surface tension have to be considered, as always, in a coating process. Some preconditions need to be met before curtain coating can be put into operation. Machinery suppliers provide appropriate test facilities in production scale to check the process in detail.
Despite the aforementioned preconditions, curtain coating offers a variety of advantages:
- High-accuracy contour coating (approximately 1% of thickness tolerance) in MD and CD;
- Contactless coating (i.e., no mechanical contact with the coating roll, for example);
- 100% consumption of coating media (i.e., no backflow);
- Suitable for high coating speeds;
- Continuous and motorized adjustment of the working width;
- No wear-and-tear parts at the coating head;
- Multilayer coatings with double-layer slot die or single-/double-/triple-layer slide dies to avoid multiple coating/drying steps are possible. This decreases investment costs (machine and building) while still allowing different functions of the different coated layers. For water-based PSA coatings, cost savings also are possible if adhesives with fillers are applied in the base layer and high-quality adhesive with all PSA functions is coated only in the upper layer.
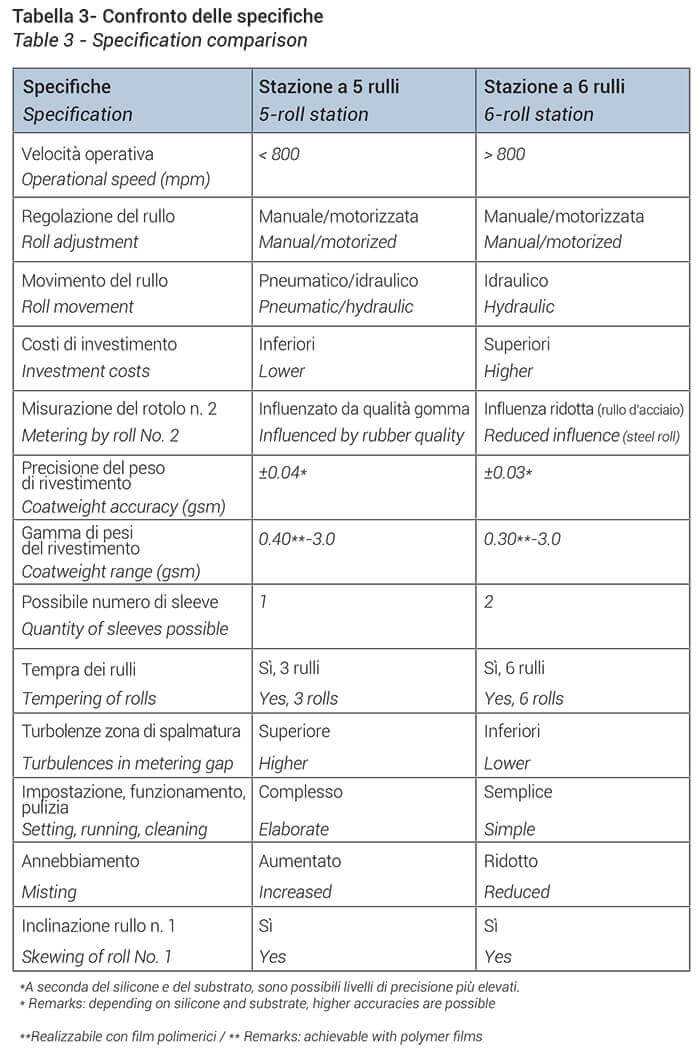
Summary
The decision of which coating system to use needs to be analyzed in depth and varies from converter to converter dependent on their product portfolio, future targets or available budgets. All aspects must be considered, and there might be, regrettably or luckily, no clear “yes or no” answer for a particular system in the beginning of the selection process. But, with the support of a qualified and experienced machinery supplier, there will be a clear, justifiable decision at the end.
By Frank Schaefer