Cifre, analisi e criteri di valutazione di una tecnologia in cui l’Italia primeggia nel mondo, tratte dal primo webinar del Gruppo Stampa Rotocalco di Acimga. Che, a riprova del grande interesse per l’argomento, è stato seguito da oltre 500 operatori di cui un quarto internazionali.
L’industria della roto gode di una vitalità superiore a quanto ne faccia supporre la (scarsa) comunicazione di settore. È un’industria che parla poco ma fa tanto – verrebbe da dire – e soprattutto che conta tanto, stando ai dati diffusi il 28 aprile durante il suo primo seminario (ovviamente via web) dal neonato Gruppo Rotocalco di Acimga – l’associazione dei costruttori italiani di macchine da stampa e converting che rappresenta tutte le tecnologie. La roto – ha documentato per l’occasione il direttore di Acimga, Andrea Briganti – gioca un ruolo di rilievo nel settore, che vale 17 miliardi di euro, del commercio globale di macchine per l’industria grafica, cartaria e del converting (dati 2019).
In questo contesto l’industria italiana gioca un ruolo di primissimo piano, attestato dall’eccellenza riconosciutale a livello globale e dalle cifre che vedono i costruttori nostrani di macchine terzi nella classifica dei fornitori dopo Germania e Cina, con una produzione 2019 di circa 60 milioni di dollari. Principali importatori: USA, Indonesia e Cina , seguiti da una nutrita schiera di Paesi orientali.
Vantaggi e limiti di una tecnologia in evoluzione
I vantaggi generati da questa tecnologia sono chiari e molto rilevanti, oggi più che mai: qualità e affidabilità si traducono nella famosa dependability che è la capacità di replicare n-volte lo stesso lavoro, con la stessa resa, assicurando così continuità nel tempo alla comunicazione di marca che i brand owner chiedono come priorità. Se usata correttamente, inoltre, la macchina da stampa rotocalco può diventare un elemento di forza nella strategia di sostenibilità delle aziende che, si sottolinea anche in questo webinar, oggi più che mia rappresenta un pilastro imprescindibile di sviluppo.
L’altra faccia della medaglia, ovvero i limiti storici della roto a confronto con altre tecniche di stampa, sono invece il costo elevato delle macchine e dei cilindri, e la scarsa flessibilità di un processo che appesantisce i cambi lavoro dimezzando la produttività degli impianti (si stima in un 50% medio il tempo di fermo per set up).
Su questi aspetti stanno, infatti, lavorando da anni i costruttori di macchine e componenti, con risultati rilevanti e nuovi progetti in fieri orientati all’ibridazione e all’efficienza. Mentre sul capitolo “costi” si è concentrata l’attenzione di Enzo Baglieri della SDA Bocconi, intervenuto al webinar di aprile per definire il corretto metodo di valutazione di un investimento a un tempo elevato e dalla vita lunghissima.
Il costo della roto secondo la TCO analysis
Una macchina rotocalco, ha spiegato Baglieri, costa in media 2 milioni e mezzo di euro classificando questa tecnologia come molto costosa. Se però ragioniamo in termini di Total Cost of Ownership (TCO) per misurare l’impatto dell’investimento sul business di uno stampatore vediamo che la valutazione cambia di molto. La metodologia è nota e richiede di considerare, anche come il costo iniziale si distribuisce lungo il ciclo di vita dell’assett acquistato e quali altri costi crea per il suo utilizzo.
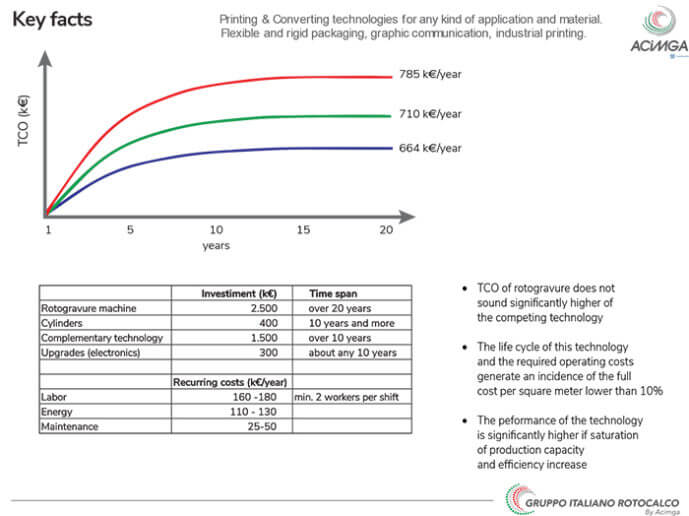
I costi spiegati a punti
Per declinare l’analisi TCO sulla tecnologia rotocalco, il docente si è avvalso della collaborazione di tre costruttori con stabilimenti in Italia e di due utilizzatori significativi. Ed ecco, facendo medie e sommatorie, cosa ha considerato:
- il ciclo di vita medio di una macchina da stampa roto è di circa 20 anni (e spesso molto superiore);
- ogni 10 anni circa si effettuano gli interventi di revamping necessari per gli adeguamenti dell’elettronica, stimati in circa 300mila euro ciascuno;
- il costo dei cilindri, che rappresentano la spesa più rilevante dell’utilizzo di questa tecnologia e vengono valutati in circa 400mila euro/anno considerando un uso di 1000 cilindri/anno al prezzo di 400 euro ciascuno (ma si consideri che anche il cilindro ha una vita lunghissima, quasi come quella della macchina);
- il recupero solventi, inchiostri e energia richiede a sua volta investimenti significativi in tecnologie complementari, stimati intorno a 1,5 milioni una tantum (anche il loro ciclo di vita è lunghissimo);
- il costo del lavoro ossia di 1,5-2 operatori per turno (in Italia si privilegiano i 3 turni su 5 giorni), che in Europa può variare fra 60 e 180mila euro/anno;
- la bolletta energetica fra 110 e 130mila euro/anno per stampare 20-25 milioni di metri di materiale;
- i costi di manutenzione, che cambiamo molto a seconda che si opti per gli interventi “classici” o i pacchetti delle assicurazioni (1% o più).
La sommatoria di questi costi distribuiti su 20 anni di vita oscillano fra 650 e 780mila euro/anno che – sottolinea Baglieri – sono tutt’altro che fuori standard. E anche il costo al mq risulta tutto sommato contenuto: considerando che una macchina rotocalco si acquista per produrre grandi volumi di stampati (anche 30 milioni di mq/anno), non supera mai il 10% (15% nel caso di piccoli lotti).