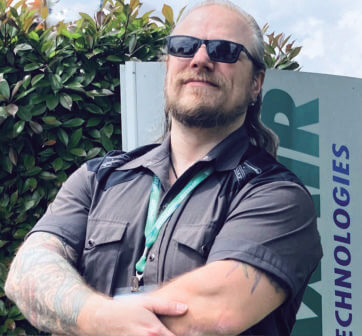
Tito Lopriore, Printing Quality & Customer Support di Linde Advanced Material Technologies
A contribuire alla discussione e a rispondere alle nostre domande è intervenuto Tito Lopriore, Printing Quality & Customer Support di Linde Advanced Material Technologies che, partendo dalla sua esperienza sui componenti, ha fatto luce su diversi aspetti della difettosità di stampa spesso associati alla gestione dell’anilox.
Parliamo di difettosità di stampa: quali sono gli argomenti che affrontate in azienda più di frequente?
Parlando di difettosità di stampa e facendo riferimento alle istanze che ci riportano sia gli stampatori che i costruttori, gli argomenti più dibattuti riguardano il ghosting, la densità fuori scala, i trasferimenti non idonei, le rigature e le barrature. Quasi mai la causa di questi problemi è ricercata nella qualità del prodotto e, in effetti, raramente questo influisce sulle criticità: oltre il 90% delle difettosità in stampa sono legate a scelte di specifiche inadatte, uso o interazioni incorrette e, in ultimo, allo stato di deterioramento del componente stesso. Nei casi di ghosting, ad esempio, un semplice corretto riequilibrio delle specifiche di incisione risulta risolutivo. Su questi aspetti è sempre augurabile che il cliente valuti le opzioni migliori in fase di specifica del set anilox: il supporto tecnico si rivela decisivo in fase di preventivo.
Altre volte è necessario lo studio tecnico approfondito per sviluppare una soluzione dedicata alla risoluzione di un particolare problema o al conseguimento del risultato desiderato attraverso il componente anilox: qui a pagare è sempre il lavoro tailor made. L’applicazione di vernici di finitura o dei primer ne sono un esempio: quando si esula dagli standard è sempre bene rivolgersi al supporto tecnico.
Va però detto che, nella maggior parte dei casi, gli anilox semplicemente non sono più in condizioni idonee a una corretta performance e una rimessa a nuovo (rigenerazione) è spesso risolutiva. Le barrature, in specie, derivano quasi sempre da errori di concentricità/TIR che hanno ormai oltrepassato la tolleranza disegno e addirittura la reale funzionalità in macchina. La rettifica o rigenerazione, infine, è in grado generalmente di riportare l’anilox all’interno delle corrette caratteristiche meccaniche.
Rispetto agli anilox, quali sono le criticità più comuni riscontrare dai vostri clienti?
Sicuramente i danneggiamenti sono i cima alla lista delle criticità più comuni: un graffio, un colpo, una inclusione di materiale duro sull’anilox viene sistematicamente riportata in stampa. L’anilox è un componente delicato: la ceramica riportata al plasma che ne riveste la tavola è molto dura, ma anche molto fragile. Le celle incise al laser hanno dimensioni micrometriche (millesimi di millimetro). Danneggiare durante la manipolazione la tavola incisa rendendo l’anilox portatore di difettosità in stampa, è uno spiacevole, a volte ordinario, accadimento. L’anilox viene, giustamente, considerato come un componente macchina e non un consumabile, ma ne va assolutamente contemplato e monitorato il ciclo vitale in funzione della qualità e delle prestazioni produttive che lo stampatore si è prefissato. La maggior parte degli anilox che vengono rigenerati lo sono a causa di danneggiamenti e non per usura.
Le rigature circonferenziali (scoring lines) sono considerate fisiologiche dell’utilizzo dell’anilox in flessografia e rappresentano un altro fattore critico di danneggiamento che si riflette sulla qualità di stampa e/o nei tempi di set up. Le concause di questo fenomeno sono molte, alcune banali e, se comprese e quindi evitate attraverso i giusti accorgimenti, minimizzano il palesarsi di questo irrimediabile danneggiamento. La perdita di performance di trasferimento solitamente viene legata alla naturale usura della ceramica, ma può anche essere legata a una pulizia insufficiente o inefficacie ed anche a una scelta non corretta delle specifiche di incisione. Un anilox che trasferisce inchiostri base acqua, ad esempio, necessita di una scelta oculata delle specifiche, che rispettino la corretta ratio volumetria/lineatura, che, nei casi più ostici, può essere coadiuvato da una scelta del pattern (disegno della cella). Un anilox che trasferisce inchiostri viscosi, con pigmenti importanti (ad esempio inchiostri UV a bassa migrazione) necessita di una apertura cella, dicasi lineatura, che sia funzionale e non di estremizzazioni non necessarie.
Secondo la vostra esperienza, cosa potrebbero fare le aziende per ridurre i problemi in stampa?
Partirei dalla parte di selezione e progettazione. Il confronto iniziale con i tecnici anilox aiuta a operare scelte opportune nelle specifiche di incisione e non dettate dall’esperienza, dal sentore o dalla moda del momento che spesso risultano errate, incomplete, non performanti. L’utilizzo di test con anilox a bande è purtroppo tuttora poco sentito, ma è determinante quando si va alla ricerca di qualità e performance ottimizzate.
Nella pratica quotidiana, ogni azienda dovrebbe adoperarsi maggiormente per una cura più attenta del parco anilox per prevenire situazioni di degrado del componente. Procedure di manipolazione e stoccaggio sicuri, verifica dello stato generale, interventi di pulizia tempestivi e frequenti, monitoraggio della volumetria sono quattro azioni cardine sui quali basare molta della lotta alle difettosità di stampa riferibili all’anilox. Una frequenza quantomeno annuale di mappatura del parco anilox aiuta a conoscere lo stato di salute di quello che è un componente chiave della macchina: ricordiamoci infine che mantenere puliti e in efficienza macchina e anilox è alla base di tutto.
Un ultimo tema da trattare è quello della formazione. Conoscerne le caratteristiche da parte degli addetti al suo uso, chiarisce concetti e sfata false percezioni garantendo un impatto sulla qualità e sulla produttività importanti anche più che la diminuzione dei danneggiamenti.
Guardando al futuro e alle innovazioni tecnologiche del settore, ci sono dei problemi che potrebbero essere risolti e diventare presto un “ricordo del passato”?
Le tecnologie di incisione hanno già fatto passi da gigante incrementando il range di lineature, migliorando la precisione e la ripetibilità delle specifiche prodotte e fornendo la possibilità di incidere disegni (pattern) di cella differenti dai tradizionali esagonali. Considerando ormai superate definitivamente le incisioni a 45° e 30°, lo standard più diffuso è ancora l’esagonale 60°, ma ormai affiancato da incisioni più performanti come quelle allungate e aperte/reverse. Queste ultime sono il punto di svolta non ancora del tutto metabolizzato dagli utilizzatori.
Come ho descritto prima, è controproducente inseguire inutili estremizzazioni delle specifiche ottenendo solo performance peggiori e difficoltà di utilizzo e pulizia. L’innovazione sta principalmente nella conoscenza, nell’utilizzare incisioni appropriate e realmente funzionali agli altri componenti macchina. In questo scenario, i problemi legati alla definizione di stampa possono ormai già ritenersi un retaggio del passato.