ZDue sta portando avanti in Italia lo sviluppo di Project Blue: una tecnologia che combina polimeri, Ctp, retini, anilox e sistemi di controllo degli inchiostri ottenendo nuovi standard di qualità nella stampa flessografica. Con molti vantaggi rilevanti anche sul piano operativo ed economico.
In questi mesi dominati dalle preoccupazioni e dalle restrizioni imposte dal coronavirus, ZDue non ha perso di vista l’obiettivo dell’anno: presentare e sviluppare anche in Italia il sistema Project Blue di cui è il partner nazionale.
Cancellato dal lockdown il grande evento di presentazione, che era stato organizzato per fine febbraio (!) al Museo Ferrari di Maranello in collaborazione con Miraclon, il service modenese di prestampa flexo ha “cambiato canale” e oggi spiega – in seminari via web e incontri con tecnici e opinion leader – essenza, utilizzo e vantaggi di questo insieme coerente di hardware, software, materiali e sistemi di controllo. Abbiamo così potuto “toccare con mano” i risultati di questa tecnologia e apprezzare un progetto che non si limita alla preparazione delle forme di stampa ma coinvolge partner e stampatori a unire competenze, impostare un metodo operativo e allineare le tecnologie, con l’obiettivo comune di stampare al meglio il packaging (flessibile, di cartone eccetera).
Perché, come tutti sanno e pochi fanno, non basta utilizzare il top dei CTP laser, una macchina da stampa “nuova e lunga”, gli inchiostri e i substrati migliori: si devono impostare dei metodi operativi con delle regole che permettono di controllare l’intero processo. Così si ottengono risultati immediati e anche ripetibili nel tempo, con quello standard qualitativo costante che non molti stampatori flexo riescono a garantire. Evitando perdite di tempo e denaro in tentativi e ristampe.
Project Blue: istruzioni per l’uso
Project Blue è una combinazione di tecnologie che coinvolge polimeri, Ctp, retini, cilindri anilox e sistemi di controllo degli inchiostri. Come tutte le tecnologie, è bene ricordarlo, presuppone una macchina da stampa e strumenti adeguati: tazza a efflusso per il controllo viscosità inchiostro, controllo del ph e della schiuma eccetera. Con questi presupposti e utilizzando un algoritmo di retinatura proprietario, Project Blue permette di ottenere una qualità elevata di immagini, testi, grafismi e logotipi, anche con basse lineature senza scalettature.
Ma i vantaggi sono molti di più: un maggiore spazio cromatico utilizzando solo i colori di quadricromia, miglior simulazione dei colori Pantone (utilizzando la Color guide/quadricromia), tempi ridotti di avviamento e asciugamento, stabilità del registro, ottima coprenza anche nei fondi pieni, un ridotto schiacciamento del punto (dot gain) e un miglior trasporto dell’inchiostro con conseguente mantenimento della pulizia delle lastre.
Pure in questo caso va sottolineato che la qualità dipende anche dal file, dato che ci sono molti modi di impostare la risoluzione, le sovrastampe, il trapping, ecc. soprattutto quando non si usi un profilo colore adatto alla separazione delle immagini in quadricromia (Fogra 39). Qui improvvisare è vietato: piuttosto che convertire le immagini in CMYK con un profilo colore a caso, e correggere la cromia dopo la conversione colore facendo danni, è meglio consegnare i file in RGB alla prestampa chiedendo la conversione con un profilo colore appropriato.
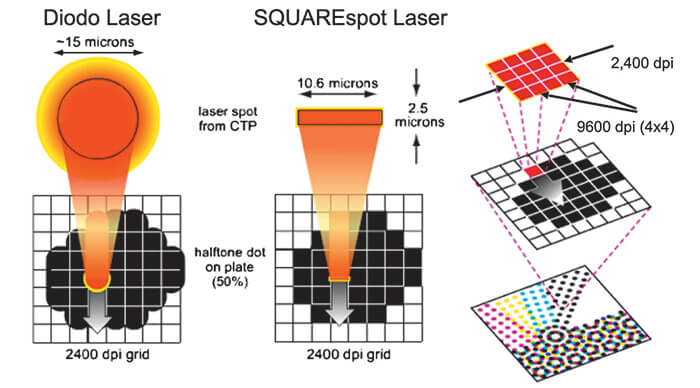
La lastra e il punto
Il polimero utilizzato per le forme di stampa (Flexcel NX) è prodotto da Miraclon che, notoriamente, ha rilevato il business Kodak Flexcel Solutions per la stampa flessografica. Per la scrittura si utilizza la tecnologia SQUAREspot pixel to pixel (figura 1), che trasferisce le informazioni dal file digitale TIFF a 1bit (o LEN) alla superficie del polimero con grande precisione, in modo che tutti i punti del grafismo siano piatti e di eguale altezza, con un miglior controllo del trasporto dell’inchiostro.
La “lastra” Flexcel NX è certificata per la scrittura a 300 lpi, permettendo di riprodurre 256 livelli per ciascun colore. Grazie alla sua struttura a cono è possibile mantenere anche un singolo punto isolato sulla forma di stampa. Si possono scegliere differenti tipologie di pattern (figure 2 e 3) che, in funzione della struttura, assicurano la stesura ottimale dell’inchiostro anche nei fondi pieni mantenendo un dot gain costante.
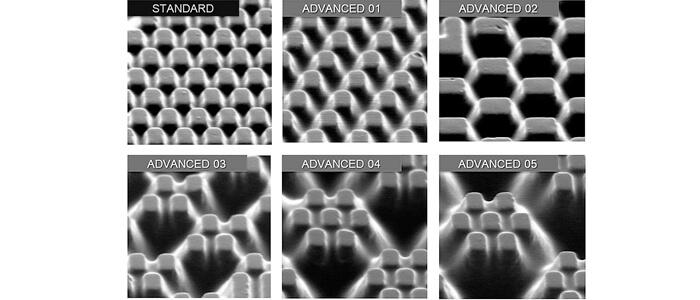
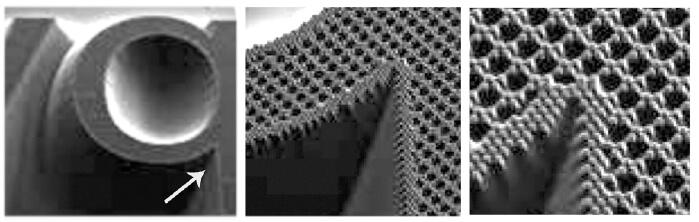
Il retino
Il retino utilizzato da Project Blue sfrutta un algoritmo che ne modifica la disposizione/geometria percentuale per percentuale e colore per colore (figura 4). A differenza del punto tradizionale, l’algoritmo utilizzato non presenta la caratteristica rosetta che può generare problemi di moiré dovuti anche a imprecisioni nelle inclinazioni dei retini, alla inadeguata scelta del tipo di anilox e in molti casi anche al soggetto da riprodurre – tipicamente tessuti, griglie metalliche, trame parallele eccetera (figura 5). Con Project Blue possiamo riprodurre una gamma tonale che inizia con un punto dello 0,4% e lo mantiene aperto nelle ombre al 99,6 % (almeno sulla forma di stampa). Maggiore è la richiesta di trasporto dell’inchiostro, minore è il numero delle “celle” incise sulla superficie del polimero, che però crescono in dimensione.
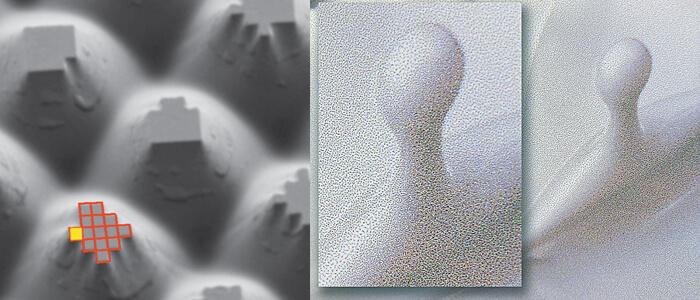
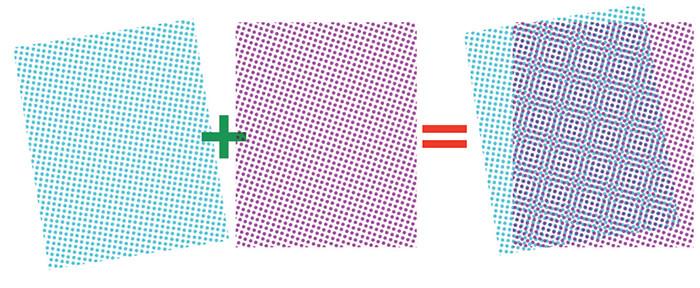
Diversi stampatori, diversi prodotti
Anche se presente in Italia solo da qualche mese, Project Blue ha suscitato un interesse concreto: due aziende già lo utilizzano per la stampa di imballaggi flessibili e altre lo stanno valutando, alla luce dei test su substrati flessibili e su cartone ondulato fatti prima dell’estate. Si tratta di stampatori molto diversi fra loro, per tipologia di stampati e per macchine e inchiostri utilizzati – a base acqua, solvente e UV (questi ultimi in beta test).
Qui dobbiamo precisare che la tecnologia di cui parliamo si articola in due varianti: Project Blue propriamente detto e Blue Edge. Il primo utilizza la forma di stampa e i cilindri anilox progettati e realizzati ad hoc da Sandon Global (rappresentata in Italia da Simonazzi). Blue Edge, invece, nasce come alternativa che permette di utilizzare i cilindri anilox dello stampatore, utilizzando non un retino convenzionale ma un algoritmo innovativo con un inedito disegno di punto, allo scopo di ottenere una risoluzione elevata delle immagini (figura 6).
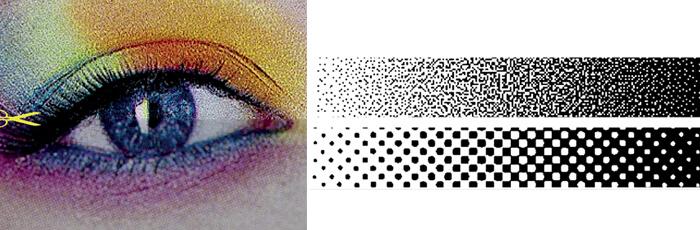
I passaggi operativi
Che si tratti di Project Blue o Blue Edge, l’implementazione inizia con la verifica di fattibilità da parte dei tecnici ZDue, che visitano lo stampatore e si confrontano sulla procedura da mettere in campo.
Il progetto prevede la stampa di una forma test specifica (fingerprint o impronta digitale, (figura 8), indispensabile per individuare retino, pattern, anilox, curva TVI, dot gain, e per valutare che tutti i componenti della macchina da stampa siano “in buona salute”.
Per ottimizzare tempi e costi, su un’unica forma test si posizionano i vari punti di controllo ripetuti con differenti retinature. Idem per i cilindri anilox: lo stesso cilindro viene inciso in più modi (a bande) con dimensioni, profondità e forme differenti delle celle. A seguire, un test di caratterizzazione dello spazio colore della macchina da stampa (figura 7). A stampa ultimata saranno evidenti i risultati migliori e le difettosità e si potranno così attivare gli aggiustamenti e le regole per avviare la routine di lavoro con Project Blue o con Blue Edge.
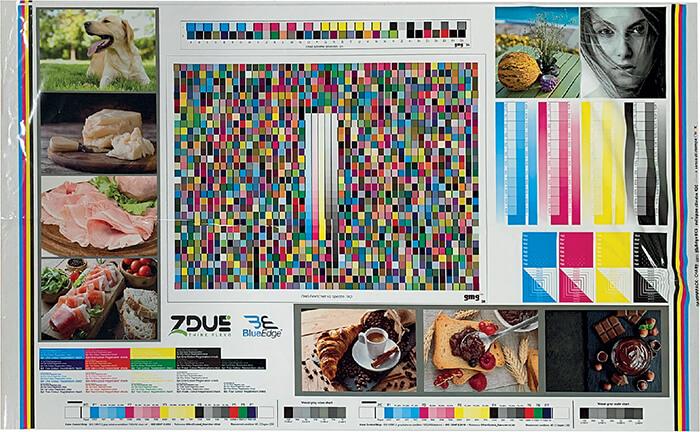
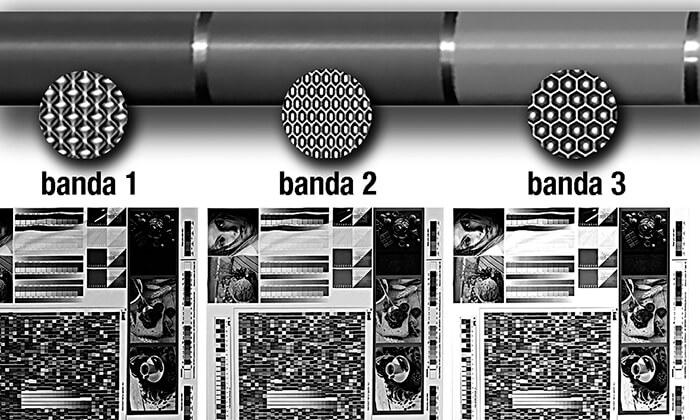