iT’s Tissue is, and always has been, all about technology: cutting edge, and experienced in action and close up. It is a unique opportunity. What follows are some of the most interesting developments that visitors will see with their own eyes when they come to Lucca from 6 to 10 June 2022.
A.CELLI
A.Celli Paper is an Italian company with 80 years of experience in tissue and paper machinery and equipment. Among the products offered by the company are complete turnkey plants, tissue machines, winders and rewinders for tissue, paper and cardboard, automatic roll handling and packaging systems and Industry 4.0 digital solutions.
With the acquisition of PMT (formerly Beloit) in 2020, the company became the leading player in the sector with 100 percent Italian ownership, extending its range of products and services to the specialty paper, graphic paper and packaging paper industries.
During iT’s Tissue 2022 A.Celli Paper will open the doors of its production plant in Tassignano, Lucca. It will be the ideal opportunity for our visitors to experience first-hand a turnkey tissue production line consisting of the iDEAL® tissue machine, E-WIND® winders & rewinders, R-WAY® Integrated solutions for automatic product handling and plant logistics, ending with a focus on Digital Solutions developed to monitor and improve efficiency and effectiveness.
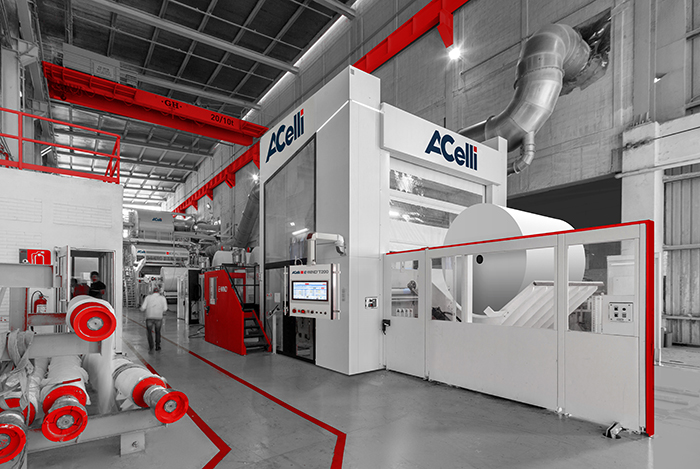
The E-WIND® T200 – part of the E-WIND® winders & rewinders product line which will feature on the line which is ready for viewing during A.Celli Paper open house at iT’s Tissue.
E80
Over the years, E80 Group has been developing state-of-the-art technologies that integrate and automate supply chain operations with the primary objective of increasing the efficiency, sustainability and safety of factories and distribution centers in the tissue industry.
Thanks to innovative technologies and a thorough understanding of customers’ logistic processes, the Group anticipated the concept of Industry 4.0 back in the 1990s. In addition to hardware systems, E80 Group has developed the SM.I.LE80 (Smart Integrated Logistics) software platform that ensures the integration of systems and flows and guarantees the total traceability of the products handled, from the entry of raw materials right through to shipping.
E80 Group’s end-to-end solutions perfectly integrate all the processes within a tissue plant.
The Group has developed a project in collaboration with Gambini to supply a fully automatic converting line. The two companies will soon introduce a cutting-edge system that brings the parent reel to the rewinder and retrieves the spent core when the operation is finished. All the operations of loading and unloading the jumbo rolls and handling the spent cores inside the unwinder will be automatic, eliminating any hanging paper reels. This fully automated operation will increase line efficiency and operator safety, as it will avoid having reels suspended.
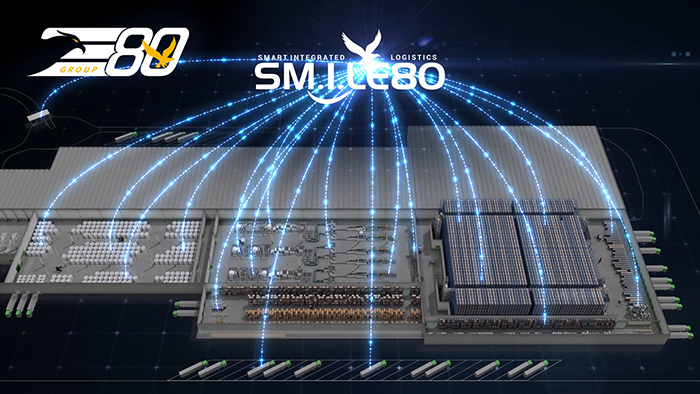
The Smart Tissue Factory – being brought to life with E80.
FUTURA
Together with Plusline, Futura will welcome visitors to iT’s Tissue 2022 by presenting the game-changing technological advances the companies have achieved together. It will also be an opportunity to celebrate Futura’s 20 years in business.
Since the last edition of iT’s Tissue, Futura has acquired Plusline and they have already transformed the nature of tissue converting automation and integration, including the development of Together, which receives the logs directly from the rewinder, and generates packaged shelf-ready rolls. The compact layout saves up to 65 percent of space for each line and an provides an unprecedented level of process continuity.
Next the embosser, and with its JOI Hydro-bond Futura has made tissue more sustainable and above all, the embosser area safer.. JOI Hydro-bond allows, even at high production speeds, the perfect adhesion of toilet paper plies with water only, thanks to the exclusive “Zero Deflexion” steel marrying roll, which compresses fibers homogeneously over the entire surface and thus fully exploits the “adhesive power” of water.
Further innovations include: a tail-sealing unit in the rewinder creating a convenient “easy-start” roll; automatic logsaw blade change and grinding; and Camallo – the first automatic solution for loading, unwinding and exchanging coreboard reels. To these we can add new unwinders, able to ensure continuous runnability with a considerable space saving requirement.
These concrete, targeted innovations, are relevant to people’s daily lives and, in the long run, will become the new market standards.
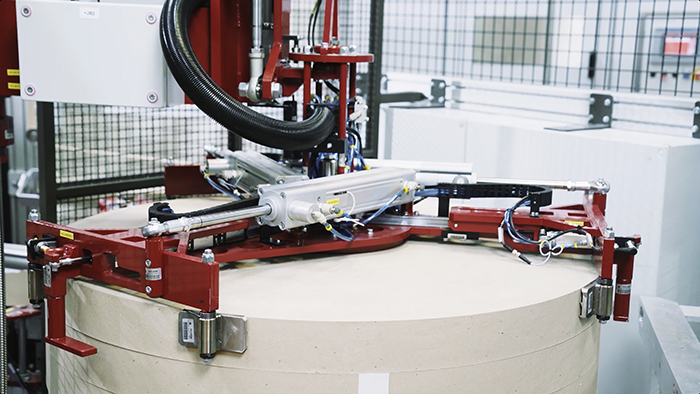
Camallo from Futura – the first automatic solution for loading, unwinding and exchanging coreboard reels.
GAMBINI
With 152 years of experience worldwide, Gambini now has 160 employees, divided between three factories, with a fourth to be completed in 2023. Among them is the TissueHub, an R&D center dedicated to the creation of unique tissue products, designed with customers and partners.
In addition, in Wisconsin USA, there is Gambini America, a commercial office dedicated to assistance and spare parts for the North and South American markets.
In June at iT’s Tissue 2022, a G1 line will be shown, complete with packaging, equipped with:
- G1: a rewinder as simple as a mobile phone
- TouchMax: the versatile reference embosser on the market
On the pilot line in TissueHub – the only full-width one – it will also be possible to see an AirMill, Gambini’s patented hot roller technology, in operation.
The open house will also feature TMC, Pulsar and Elettric80, which have numerous projects in common with Gambini: one of which – concerning unwinders – will be unveiled during the event.
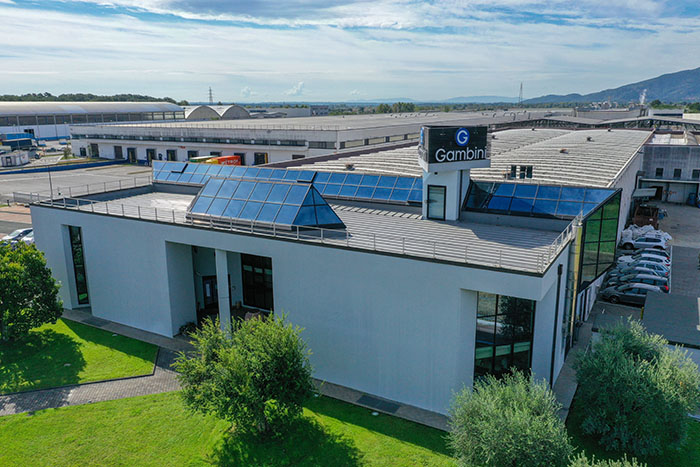
See G1 and TouchMax among technologies demonstrated at Gambini
KÖRBER GROUP
Körber Business Area Tissue is transitioning from a machinery supplier to a strategic partner providing technologically advanced and integrated solutions through the Körber ecosystem.
In this revolutionary market approach, the technologies involved in the entire tissue converting process are now integrated into a single solution, from raw paper to finished product, right up to distribution logistics.
In the Körber ecosystem all the machines making up the production line, from parent reel unwinding to palletization, including those developed by companies external to the Körber Group, are connected to each other and controlled by Sam Flow, a dedicated piece of software that continually monitors the process and is capable of self-adjusting the main production parameters to deliver the maximum production efficiency.
During iT’s Tissue 2022, it will be possible to view examples of how individual machines communicate with each other to obtain the maximum production efficiency. In particular, Körber will present the new Perini Vega S8 lines for converting large diameter rolls typical of both “away-from-home” and consumer products, MTC ITF Change for interfolded products featuring an easy cut-off format change, which is possible by simply replacing the drawer containing the folding rolls, and Casmatic Zephyrus for packaging roll and folded products with recycled cardboard boxes also in mixed format – a sustainable concept dedicated to the e-commerce channel, and the PA15 solution for innovative, fast and flexible palletizing.
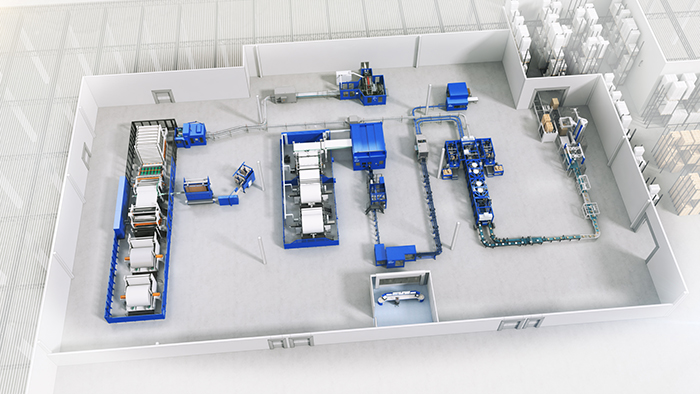
Körber will show how individual machines communicate with each other to obtain maximum production efficiency.
OMET
Among the new technologies OMET will present to the next edition of iT’s Tissue, 6th-10th June 2022, is the revolutionary RED Line, the new converting line for increased production. Thanks to a new servo-controlled cutting unit, specifically developed by OMET to reduce waste and time, this machine doubles the usual production, thus reaching up to 10,000 napkins per minute. Live in demonstration will be also the MF Line, the OMET multi-folding machine with a vacuum/mechanical folding unit that provides the maximum flexibility in terms of folding options.
The innovative ASV Line, the easy-to-use and highly modular OMET machine for the production of high-speed interfolded tissue products will also contribute to the event with its new technologies! But the real turning point is the new XV Line, the revolutionary machine designed by OMET to increase the production capacity and the efficiency of the entire converting process. This line is the result of a careful technological research with innovative and patented operating principles that allow for an absolute modularity of the machine itself.
This high productivity line can reach up to 25,000 pieces per minute. Don’t miss this opportunity.
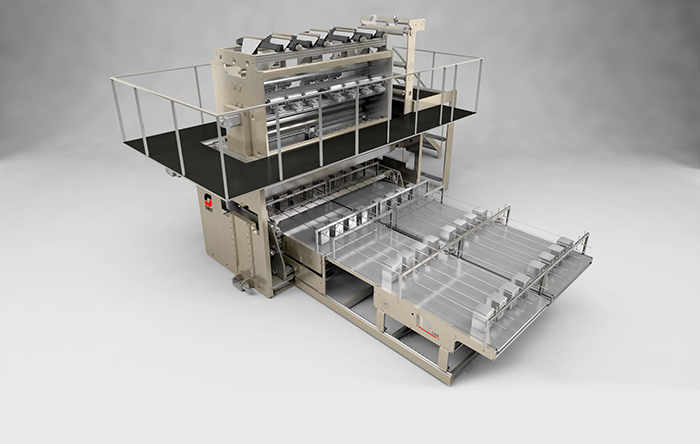
Omet XV – the real turning point
PCMC
After decades mastering center winder technology (Centrum) and perfecting surface winders (Forte), PCMC began asking some thought-provoking questions about winding. What if the logs did not have to climb uphill to get into the winding nest? What would be the best way to wind and support a log preserving bulk and caliper? What winding technology could merge the advantages of surface and center winding removing the disadvantages? Which wind nest design could be inherently robust to process material variations and, at the same time, be the easiest to run for the operator?
The answer is PARAGON, a new high-speed rewinder with a new winding concept that only PCMC could have created.
PARAGON employs a revolutionary new winding nest with center drives and a winding belt beneath the product which affords exceptional control and support for the logs from winding start to finish, as well as superb caliper retention of the wound web. It is innovative yet easy to use thanks to SmartTOUCH, the clean and modern interface that offers enhanced smart features.
PCMC’s history in tissue converting dates back nearly a century. PARAGON combines leading technology from PCMC’s proven Forte rewinder with an innovative, patented winding design, initiating the dawn of not just another century, but also of a new era of rewinding.
During iT’s Tissue PCMC will also present a top-category packaging and palletizing line as well. Both solutions together will lead to a clear increment in product quality and performance.
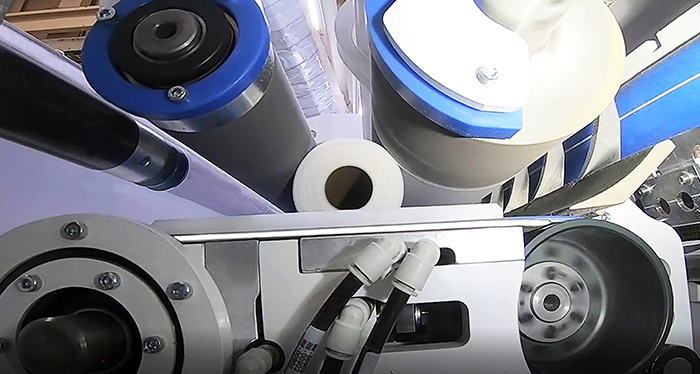
PCMC’s PARAGON features a revolutionary new winding nest
PULSAR
For iT’s Tissue, Pulsar Engineering will unveil Darwin and Antares, an evolution in the tissue industry.
The Darwin project started in 2015, when Pulsar decided to bring into the Tissue Industry concepts that were new for this sector but known, developed and applied in other industries. The goal was to create a system that replaces the current ones with new technologies in order to revolutionize the packaging and palletizing process for the factory of the future, linked to the ecommerce world. Antares is part of Darwin: it is a pack and pallet system from secondary packaging.
During the event, Pulsar Engineering will show the latest developments on its conveyors components and layouts, in line with rolls production equipment.
Pulsar Engineering will also present the latest developments and performance achieved with the PLS DYNAMIC platform, a Digital Twin line’s generator, to virtually anticipate the real line’s performance and behavior.
Together with the conveying systems, the Quatis Rolls and Quatis Pack, quality and compliance checking machines for unwrapped and wrapped products, will be shown at work. It will also be possible to see the new Quatis Pocket, the latest model in the Quatis series for quality inspection. Its small dimensions allow it to be installed on one line in just 20 minutes and to be easily transported in two wheel cases.
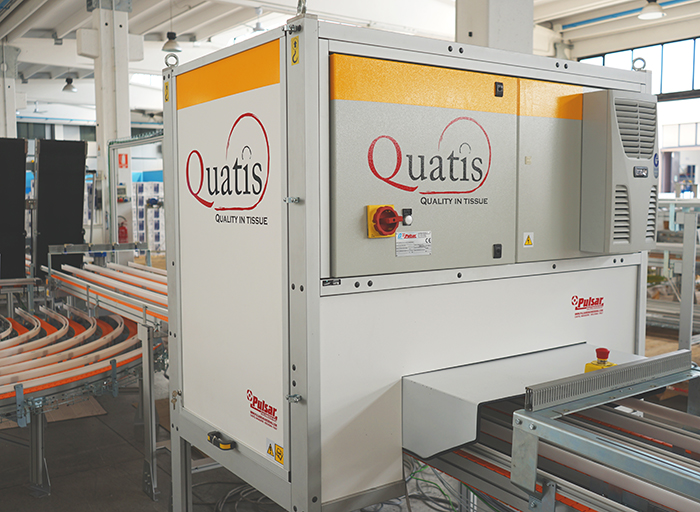
Pulsar’s Quartis series takes care of quality and compliance – it is among many technologies being demonstrated by the company at iT’s Tissue.
RECARD
A new entry in the Recard product range is the headbox HP, a high-performance headbox specially designed for very low basis weights (8.5-9.5 gsm uncapped).
Recard has also recently introduced a steel-shell Yankee to the market with a great thermal exchange efficiency and relatively low investment cost.
Furthermore it is a must to mention the unconventional shoe press proposed to complete Recard’s press section family, which is mainly composed of a single suction press or double press (suction followed by blind-drilled press). This is an application of the shoe press that differs somewhat from the solutions available on the market.
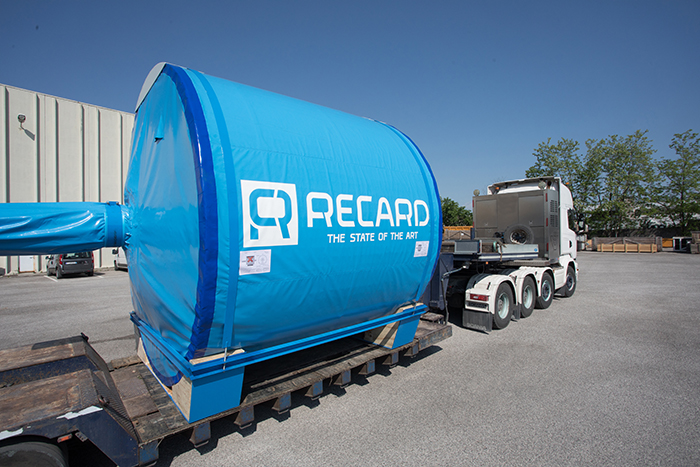
Shipping one of Recard new steel-shell Yankees.
IMA TMC
Today’s market is demanding wrappers that are flexible and able to produce a wide range of products, including those overwrapped in poly or paper. The need is also for fast machines, with a single wrapper able to process the production of a full-size rewinder, while maintaining ease of use, especially considering the high turnover in the current labour market. Just-in-time production is also required: the ability to switch batches of production in minimum time, keeping raw materials and warehouse costs to a minimum. Last but not least: sustainability, where TMC has also shifted its focus to in the past couple of years, recently introducing the first wrapper able to wrap rolls in paper. To answer to the above market requests, IMA TMC has launched WRAP250: a huge leap in wrapping technology.
WRAP250 not only leads to a 25% increase in production speed (up to 250 ppm), with a smaller footprint, but it also includes multiple technology improvements, such as quick changeover and the never stop concept, to allow the wrapper to automatically check and discharge non-compliant roll configuration. In addition, the PUSH-PULL overhead trolley allows better and easier control of the pack while it moves to a different section of the wrapper. IMA TMC WRAP250 is the answer to all current market needs.
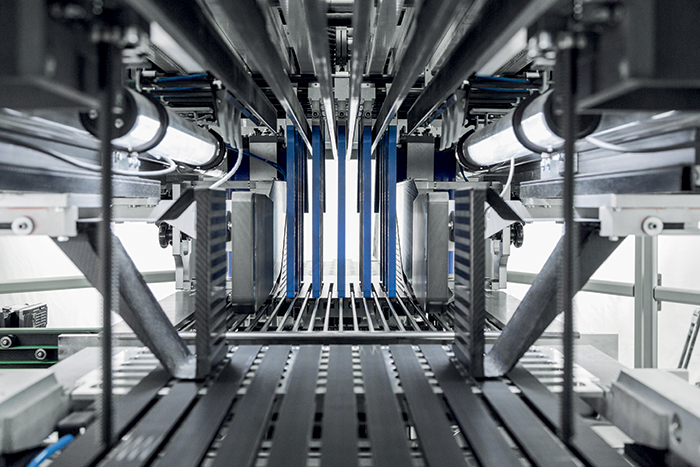
WRAP250 not only leads to a 25% increase in production speed but also includes multiple technology improvements
TOSCOTEC
Toscotec will showcase major technological breakthroughs designed and manufactured for the tissue mill of the future.
Toscotec will present a brand-new tissue machine concept designed to produce both conventional and premium quality structured tissue paper with significantly reduced operating costs.
Toscotec’s showcase will also include a new generation design TAD machine featuring an innovation that delivers a significant reduction in energy consumption, thereby boosting the energy efficiency of premium-quality tissue production.
In the space of green energy, Toscotec will introduce two disruptive innovations: a new design Steel Yankee Dryer powered by alternative energy that is set to become a game-changer in the tissue industry, and 100% hydrogen burners for the Yankee hoods of the future.
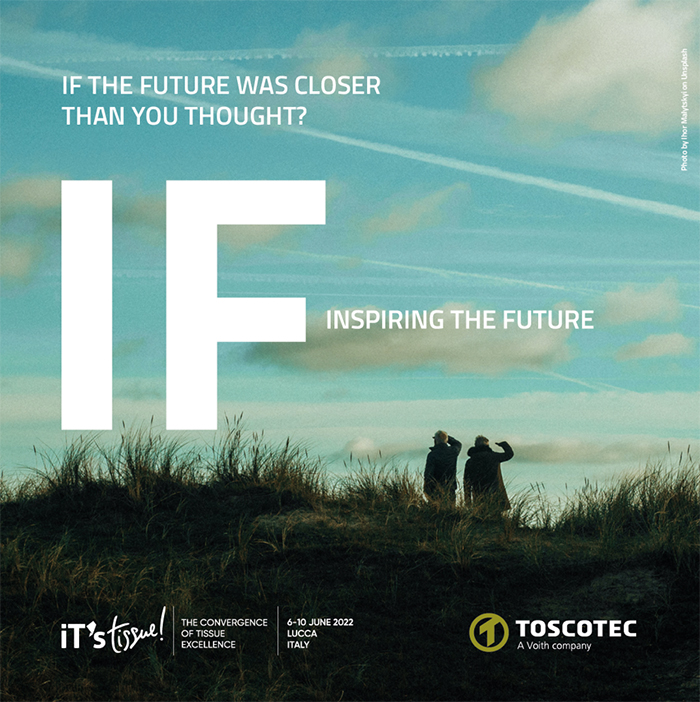
Expect disruptive innovations from Toscotec