When Drorys Packlist S.p.A. decided to upgrade its print and lamination capabilities, the Italian label and packaging specialist turned to BOBST. With the addition of a high-speed BOBST gravure press and a multi-technology laminator, the company is now extending its presence in the flexible packaging market.
Over the past decade, Drorys Packlist has built a solid partnership with BOBST, investing in both gravure and flexo print technology from the Swiss manufacturer. The most recent acquisitions include a BOBST RS 6003 gravure press with nine print stations and a BOBST NOVALAM 800 laminator bought to extend further into flexible packaging with best-in-class equipment. The new machines have joined two BOBST MASTER M5 inline flexo presses that serve the company’s many label customers.
“Our relationship with BOBST has gone from strength to strength, giving us the capabilities required to succeed in a very competitive market”, commented Gabriele Brocani, CEO and son of the founder, Piergiulio Brocani. “Our latest investment with BOBST is very exciting, being made as we embark on a new chapter in our company’s history.”
Experience and innovation
The foundation of Drorys Packlist dates back to 1945. Today, the company employs 75 staff and records an annual turnover in excess of €20 million. Headquartered in Turin, with a second production plant in Palomonte, Salerno, its strong expertise lies in the printing and converting of high-quality self-adhesive labels, sleeves and flexible packaging. Since the very beginning, Drorys Packlist has been a trailblazer in creativity and customer service.
“The type of knowhow we have simply can’t be bought, it only comes with years of experience and hard work through constant research and development”, said Mr Brocani. “We continue to innovate to deliver products that satisfy our big brand owner customers, which include Ferrero, Unilever and Heineken, across Italy, Europe, North America and further afield. For that, we must partner with the industry’s leading equipment and solutions suppliers, such as BOBST.”
Faced with demands for maximum quality products at lower prices and faster service, Mr Brocani and his team chose BOBST machinery due to the high level of automation, impressive speed, excellent build quality and ease of use. He explained: “We are busy expanding our business beyond labels into flexible packaging, we are certified to meet food packaging standards with BRCGS and we are offering all solutions – from mono-materials to laminated structures, from paper and aluminum to PP, PE, and PET – so versatility was a key factor in the selection process. Our new BOBST gravure press and laminator fulfil these criteria perfectly, giving us the flexibility, strength and agility we need”.
Meeting sustainability demands
As the market moves towards the use of more environmentally friendly products and manufacturing methods, Drorys Packlist also sought equipment that could help reduce its carbon footprint.
“Green solutions that help achieve sustainability targets are a key priority for our customers, so we must provide solutions for them that satisfy those needs”, stated Mr Brocani. “Our BOBST machines come with automated features that help reduce waste, save time and lower the energy usage in everyday production. This is also essential for our future growth because the market wants assurances that we and our packaging products are sustainable.”
With its lean and compact design enabling a shorter web path, the BOBST RS 6003 gravure press creates around 30% less material waste at start up, compared to traditional machines. Energy consumption is also significantly lower thanks to the dryer which has air nozzles on both sides for even and faster drying. Its Registron® register control system and Total Automatic Pre-register Setting (TAPS) offer automatic pre-register setting to minimize waste of materials, inks and operator time. The Flex Trolley reduces job changeovers to 2.5 minutes per unit, with the flexibility to change either the complete inking system or just the cylinder itself.
The new BOBST NOVALAM 800 laminator is engineered to accommodate a wide range of film and paper substrates, including conventional materials and those optimized for recycling. Designed for ease of operation, this versatile laminator supports solvent-based, water-based, and solventless coating, and comes with Registron® Mark-to-Mark reading technology for in-register cold seal and lacquers. Coatings are applied through a multi-trolley system that enables fast job changes with minimal waste without the need for any special tools.
Ensuring enduring success
To ensure maximum equipment utilization and guarantee that customers receive their deliveries on time, Drorys Packlist purchased a maintenance package, which includes remote service, from BOBST. This decision has already proven invaluable by keeping the machines at peak performance and eliminating unwanted stoppages.
“We have had a great experience with BOBST services in the past and wanted to continue safeguarding our productivity”, Mr Brocani recounted. “The option to connect to the service team remotely is particularly useful. It allows us to get started again quickly, if we encounter an issue. Thanks to this great feature, the machines will quickly return to production and downtime is considerably limited, without an engineer having to visit.”
Commenting on the partnership, Alberto Vaglio Laurin, Southern Europe Flexible Pack ZBD, said: “Drorys Packlist is a leader in the Italian market and we’re very proud to work with the team, supplying both equipment and services to support them. Pairing the BOBST RS 6003 gravure press with the NOVALAM 800 laminator gives Drorys a fantastic competitive advantage that will ensure successful growth in the flexible packaging market.”
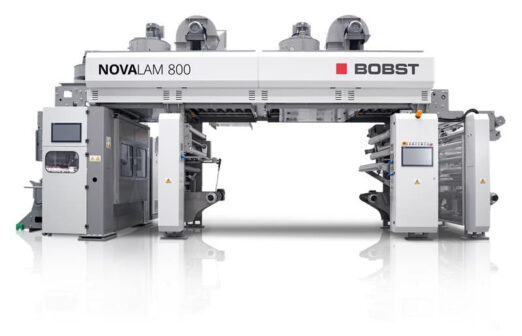
BOBST NOVALAM 800