Simec presents at K the latest version of Caboll Print: a line of rollers for various converting applications. Radically innovative, it exploits the prerogatives of a novel coating with unprecedented performance. Tested in collaboration with major manufacturers and printers, it is told to us in this interview by Emilio Della Torre, CEO Simec Group.
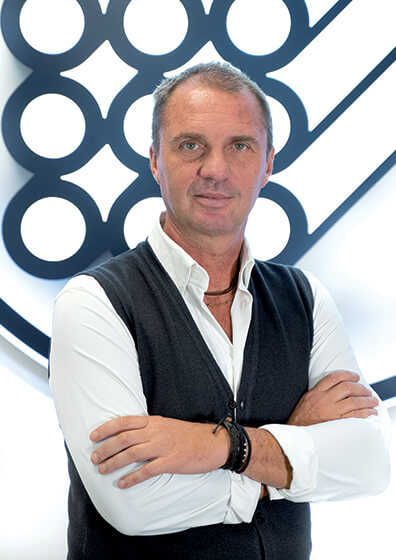
Emilio Della Torre, CEO Simec Group
Simec presented Caboll at the last Print4All 2022, where it attracted lively interest and curiosity but occupied a discrete space, far from the limelight. Now in K it dominates the scene. What has changed? And what is it all about?
Caboll is an elite product, and at Print4all Simec Group decided to introduce it to its loyal customers. Since Caboll can be used in various applications in the converting industry, we took advantage of the fair for very in-depth comparisons and specific focuses with our customers.
Nothing actually changed on our sales strategy. The period between Print4all and K allowed Simec the completion of the production structure dedicated to this specific product, and to further deepen our knowledge about the product’s performance.
I specify that Caboll is actually not “a” product but a line of anilox rollers for different applications. With Caboll, Simec Group introduces to the market a multi-purpose product that, thanks to an innovative deposition process and specific processing peripherals, can be used according to different post-coating processes on many different types of rollers, bringing concrete benefits compared to other types of coatings, such as galvanic or thermal spray.
Here we talk specifically about the latest version of Caboll Print. How does it differ from a ceramic anilox roller?
The latest structural evolution of the anilox occurred with the introduction of chromium oxide and laser etching. Since this transition, attempts have always been made to compensate for the product’s operating problems by developing new etching geometries, which have marginally solved the problem. This is because the structural characteristics of chromium oxide promote clogging of the cells and thus frequent roller maintenance and sudden changes in the transfer to the printed matter.
So we focused a lot on different solutions, oriented toward researching alternative types of coatings and new application systems, with the goal of obtaining coatings with no porosity, hardnesses equal to or higher than a chromium oxide, and excellent corrosion and etch resistance.
The absence of porosity of the coating allows almost all of the liquid contained in the alveoli to be released; this increases the density on the mold and improves dot definition on the lows, drastically reducing cleaning operations.
The most innovative element is therefore given by the material used for the surface coating, the result of Simec R&D, which has no equivalent on the market and ensures unprecedented performance. Which ones?
The Caboll product introduces important innovations in the material application system, and for this aspect the collaboration with our technology partner FlameSpray is of paramount importance. Simec Group has always opted for In Plant solutions, not investing directly in deposition systems but leaving the technological and production aspects under the management of world-leading companies in this field. All this allows us to have not only specific R&D, but also constant plant turnover, which is not possible for 90% of our competitors.
The technological development developed by Simec Group has focused on all the solutions related to the processing of this type of coating, with different preparation and surface processing lines depending on the application sector for which the product is then intended.
With what types of ink and substrate? With differences in quality outcome and process speed?
Caboll Print has been tested in different applications and with most of the inks and substrates in use on the market. As with all new products, the amount and specificity of testing was geared primarily toward defining the technical characteristics of the process and determining the characteristics of the etchings for the different types of machines and applications.
The development was carried out in collaboration with manufacturers and printers, so that the needs of both could be understood and not only the performance in printing but also the maintenance and response of the product with different types of plates or doctor blades and under production operating conditions could be evaluated.
The benefits highlighted by customers who are using Caboll Print have been very similar across all applications.
Does Caboll Print serve “only” label printing or all areas of printing? In what other areas can it be used?
Caboll Print can be used in any application where a roller is required to perform a liquid transfer function, so in flexographic, gravure and offset printing.
Also in the converting sector, and again under the Caboll brand, Simec Group offers the Coat version, intended for applications such as laminating, coating and laminating.
Caboll will thus be used in a wide range of sectors.
In this period of shortage of materials and components are you able to secure supplies?
We are certainly experiencing a very difficult period both in terms of the supply of raw materials and components and the extreme variability of their prices. Simec Group addressed this problem through a primary customer needs management system; thanks to the data recorded in this system, we were able to size our warehouses of semi-finished products and raw materials. The next issue was to adapt supply to new market conditions and, from this perspective, to search for new business outlets that would accept the changes. In essence, our warehouses have most of the process materials and semi-finished products to support market demand.
Simec has built a name for itself as an innovative company on all fronts of product design and management. On Converting, we had given an essay on this in an article devoted to servitization in an Industry 4.0 context (see QRcode). In the case of Caboll Print, what gave “the La” to the project? What figures were involved and the underlying market vision?
We believe that the future of an industrial market such as the one where we operate will require manufacturers to transform their role-from product suppliers to suppliers of solutions that are increasingly tailored to specific plants or user needs. Simec Group has long invested heavily in this, developing systems that enable predictive management of its warehouses, based on the durability of its products depending on the type of printing press and the activity of its customers. All this has led to the development of software dedicated to product life reporting, which allows customers to accurately calculate the real operating cost of rollers and sleeves and to manage their anilox fleet by reducing the amount of regenerations due to errors in maintenance, screen selection and storage.
We are also doing a lot of work on maintenance processes; we have acquired patents on non-invasive cleaning systems and systems for remote diagnostics.
What expectations do you have in terms of geographic spread and outlet sectors for the new anilox?
Simec Group already operates globally for most of its products. We believe that Caboll will strengthen the company’s role with loyal customers and enable it to further extend the installed base, similar to some of the products in the HQ lines such as embossing rollers or special rollers developed and customized with leading plant manufacturers, with whom we share distribution worldwide.
Today we are not yet in a position to determine in which specific sector this product will accelerate most rapidly. Certainly the investment, which is already operational, is able to meet not only in size but also in quantity the demand.
Caboll will not only be available in the Print version; we expect high demand for other versions of the product as well, intended for special applications where, at the moment, there are no technologically comparable alternatives.
New projects? What is Simec R&D engaged in now?
Simec Group operates in 56 application areas, which is why it is committed to ensuring continuous innovation of all its products. This is accomplished through close cooperation with leading plant manufacturers, who find in our company the ability to innovate by carefully following their needs. Simec Group devotes most of its resources in this direction; we can definitely say that Simec research today is oriented to the technological conversion of products, such as Caboll, that ensure performance and reduced environmental impact, introducing new concepts of circular economy that provide for the reuse of products thus extending their life. We consider this to be particularly important at a time in history where cost and availability of raw materials are a problem for the entire industrial sector.