Gli skill perduti e il valore della collaborazione
È un mondo, quello del mercato flexo, direttamente correlato a quello del packaging flessibile e dunque condizionato da due fenomeni trasversali. Da un lato, da Greta in poi, dalle pressanti richieste di sostenibilità dei brand owner, e dall’altro dalle nuove dinamiche del mercato del lavoro, dominate dalla penuria di personale specializzato e dalla scarsa propensione delle giovani generazioni a “sporcarsi le mani” sulle macchine.
Una rivoluzione, insomma, che ha costretto le aziende a cambiare, come mostra la stessa Bobst, uscita dal perimetro tracciato da 130 anni di cultura famigliare per aprirsi alla collaborazione con altri leader di filiera in tutto il mondo. Con una visione, sottolinea Sara Alexander, di lungo respiro e un obiettivo di lungo respiro: «contribuire fattivamente a costruire un packaging migliore per un mondo più sostenibile, dove una plastica nuova possa svolgere la sua insostituibile funzione di protezione e conservazione degli alimenti senza più creare scompensi nell’ecosistema».
Slogan e risultati: il mercato flexo chiede concretezza
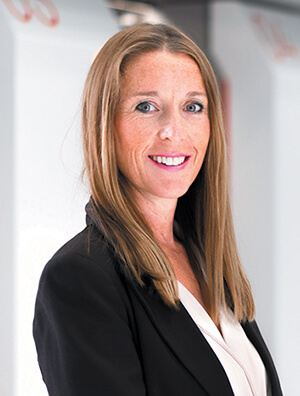
Sara Alexander
Uno sguardo agli orientamenti e ai risultati conseguiti da Bobst in ambito del mercato flexo ci offre l’occasione di notare un altro fenomeno recente, che potremmo definire come la “messa a terra” dei grandi principi del marketing. Quelli, per intenderci, a cui si ispirano anche i 4 pilastri della Visione di Bobst (e, variamente declinati, delle altre industrie impegnate a creare valore in questo mondo che cambia): sostenibilità, automazione, digitalizzazione e connettività. Fino a poco fa spesso sembravano astratti e retorici ma ora il loro significato è più chiaro grazie all’avvicinamento fra teoria e pratica imposto da un mercato che, sottolinea Alexander «vuole risultati concreti.
Per i brand la sostenibilità non può essere solo un discorso ma deve tradursi in meno scarti, minore consumo di energia e nuove strutture plastiche eco sostenibili». Si chiarisce così anche il rapporto fra queste “parole d’ordine”, dove Sostenibilità incarna il principio guida e automazione, digitalizzazione e connettività creano le tecnologie abilitanti.
Nuove macchine per nuovi materiali
Ciascun imballo è un ecosistema dove tutti gli elementi sono in relazione fra di loro: quando ne modifichi uno devi cambiare anche gli altri. Così, per creare packaging sostenibili occorre trovare nuovi substrati gestibili a fine vita, nuovi inchiostri, nuovi adesivi, nuove soluzioni barriera. La “prova del 9” si fa sulla macchina da stampa che, ovviamente, sarà stata a sua volta ridisegnata ad hoc, dove tutto deve girare bene.
Le strade possibili sono moltissime, e la stessa Bobst ne percorre più d’una, spiega Alexander: «Con diversi gruppi di partner siamo partiti, già da anni, a esplorare le nuove frontiere dei laminati monomateriale a base PP o PE, che permettono di creare packaging barriera altamente performanti e interamente riciclabili, con benefici economici e ambientali rilevanti. Abbiamo da poco presentato i risultati della seconda fase di sviluppo di una serie di “prodotti hero”, documentati da test davvero interessanti (1); ora stiamo iniziando a lavorare sui base carta e ad “aggredire” il vasto regno dei polimeri biodegradabili e compostabili, molto sfidanti per il costruttore di macchine».
«In ballo – spiega Carrara ci sono velocità, temperature, inchiostrazione… moltissimi aspetti che in flexo è più facile controllare, facendo di questa tecnologia l’apripista di nuove applicazioni. Basti pensare alla sensibilità alle alte temperature di molti nuovi polimeri, che la struttura compatta di una macchina a tamburo centrale permette di minimizzare, governando un fattore che influenza moltissimo il registro colore e, indirettamente, anche la velocità del processo».
I traguardi del waterbased
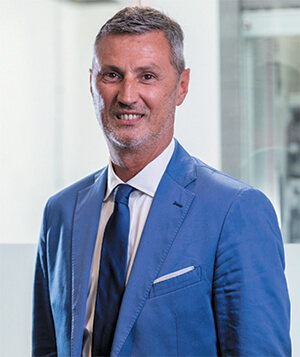
Marco Carrara
Da questo punto di vista, i 600 m/min sul film polimerico stampato ad acqua raggiunti da Bobst sulla Expert CI rappresentano un traguardo particolarmente significativo sul percorso, virtualmente infinito, di una sostenibilità compatibile con le esigenze dell’economia industriale avanzata.
«A noi spetta il merito – rivendica Carrara – di avere saputo tarare ogni elemento del processo sulle caratteristiche dei nuovi substrati. Ma non vi sono dubbi sulla centralità del passaggio dal processo a solvente (con cui tutt’oggi si realizza l’85% delle stampe flessografiche) al più sostenibile base acqua, e sul merito dei produttori, dalla cui capacità dipendono direttamente la resa ottica, l’adesione al film, la resistenza all’abrasione dei nuovi inchiostri». Bobst lavora con diversi partner sia in mercato flexo sia in roto «e con Follmann, a Bielefeld abbiamo ottenuto dei risultati straordinari di qualità, consistenza e velocità».
Sostenibilità fa rima con velocità (o no?)
Nella transizione a un packaging più ecologico il ruolo della tecnologia è fondamentale ma non sempre sufficiente. Guardiamo l’ECG, ad esempio: la sua diffusione non è proporzionale alla sua efficacia ambientale ed economica. I motivi sono disparati e vanno dallo scarso entusiasmo degli inchiostrai (con l’ECG si usa meno inchiostro, Ndr) alle esitazioni dei converter nostrani che, facendo realizzare i cliché all’esterno, non controllano direttamente il processo e dunque neppure la qualità del risultato. «Nelle Americhe – nota Carrara – dove i brand owner hanno il potere di imporre le scelte a loro più convenienti, l’extended color gamut è molto più diffuso; inoltre la dimensione dei converter è tale che possono dedicare parte delle macchine all’ECG e parte ai colori speciali, senza dover fare scelte radicali».
Anche la velocità, avverte il manager, che è una manifestazione di eccellenza tecnologica, non è un valore assoluto. «Fischer & Krecke aveva realizzato già ai suoi tempi una macchina capace di girare a 1000 metri/min ma oggi, con la progressiva riduzione delle tirature, anche gli 800 m/min della nostra Master CI hanno un’utilità limitata, in settori di nicchia con grandi volumi e tirature ancora lunghe. Essere sostenibili vuol dire anche cambiare mindset e accogliere il principio che “il massimo” non è comperare troppo se ti serve poco: anche la macchina da stampa va dimensionata q.b. – quanto basta – altrimenti è uno spreco».
Quei 20 m di scarto e gli 80 motori a 110 Kw
Alla domanda su dove viene orientata la R&D Bobst in ambito flexo, la risposta è immediata: «sulla standardizzazione e automazione del processo, per ridurre scarti e consumi». Il sistema smartGPS (Graphic Positioning System) di Bobst, ricorda Carrara, è il benchmark dell’industria in fatto di settaggio automatico del registro e delle pressioni di stampa, e svolge un ruolo rilevante nella riduzione degli scarti di avviamento. È grazie a sistemi come questo che il gruppo svizzero può vantare risultati eccellenti, come i 20 metri di film srotolati davanti alla macchina da stampa, in una delle ultime demo pre covid. Un dato tanto più importante quanto più le tirature si riducono e costosi sono i substrati di stampa, come le nuove plastiche alternative.
Coerente il capitolo sempre aperto della riduzione dei consumi energetici, dove l’industria continua a fare passi avanti da gigante supportata da fornitori in marcia verso motori classe AAA+. «Una stima fatta di recente insieme a un cliente salvadoregno, comparando una nostra macchina a ingranaggi del 2003 con la nuova gearless da 80 motori, valuta i consumi di allora a 140 Kw contro i 110 Kw (e le prestazioni in più) di oggi», riferisce Carrara. Che precisa: «Naturalmente non è tutto merito dei fornitori. I progressi che abbiamo fatto, ad esempio, nelle tecnologie di essiccazione e di accoppiamento, hanno generato una enorme riduzione dei consumi – energetici e non solo. E anche una serie di soluzioni astute, ad esempio per non disperdere il calore prodotto da alcuni elementi della macchina, per trasformarlo in energia utile ad altri. Anche in questo siamo piuttosto bravi».
Il fattore F (formazione)
Il cerchio si chiude quando il capitolo automazione si ricollega a un tema toccato all’inizio di questa conversazione, ovvero la necessità di rendere le macchine sempre più “user-friendly” per poter essere gestite anche da personale poco specializzato. «Il problema – precisa Marco Carrara – non riguarda solo la formazione delle nuove reclute, ma anche la coerenza di prestazioni del personale nel suo insieme, pena il rischio di ritrovarsi con un output diverso in ciascuno dei tre turni di lavorazione…».
Per venire incontro a un’esigenza che si fa sempre più pressante, Bobst non lavora solo sulle macchine. Grandi investimenti sono devoluti a dotare ciascun Competence center di macchine a disposizione degli stampatori e dei brand, per fare test e progettare sviluppi, ma anche di tecnici dedicati al training del personale del cliente. «Durante il lockdown i corsi si facevano da remoto, ma questa settimana a Bielefeld ho appuntamenti tutti i giorni, e domani, dopo due anni, vedrò per la prima volta un cliente sudamericano. Sarà una grande gioia».